Supplier Resource
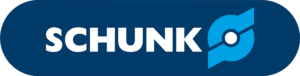
When handling delicate parts, a pneumatic gripper is often overlooked because it might develop too much force and damage the part. Vacuum or force-controlled electric grippers are sometimes the first choices in such applications. But when factors such as surface irregularities or part position repeatability make vacuum solutions impractical, and high costs of electric grippers make them undesirable, we have an alternative with the SCHUNK KTG 50 Two Finger Parallel Gripper.
Component Breakdown
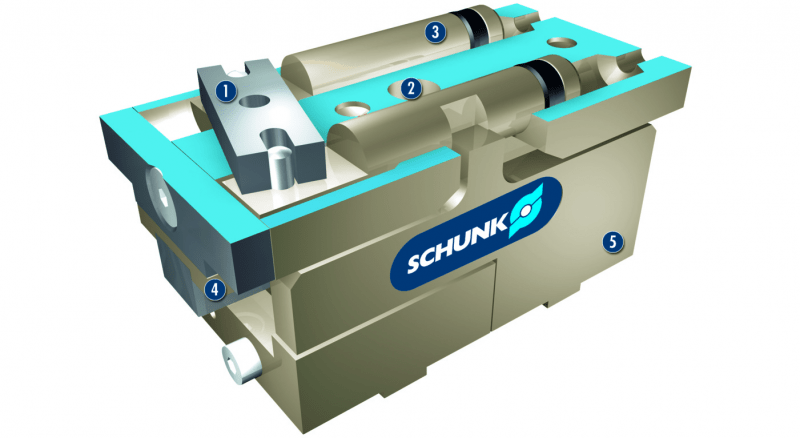
In the picture above, the Lever Principle Kinematics (1) synchronize the jaws smoothly with low friction and keep them centered with high repeatability over the 4.5 mm stroke per jaw travel. The Hollow Center Bore (2) gives users the capability for adding peripherals such as sensors, part ejectors, or optical part recognition devices. The Double Piston System (3) with its low friction seals and small bore diameters allow this gripper to operate at pressures as low as 1 bar or 14.5 psi, which translates into a gripping force of fewer than 0.5 pounds. The Profile Rail Guidance (4) gives this gripper high precision with no backlash and low friction. And the High Strength Aluminum Alloy Housing (5) keeps the weight of this gripper to under 0.08 kg, or a little less than 3 ounces.
The video below demonstrates how we can dial down the air pressure to this gripper for a very light gripping force.
If you’re handling delicate parts and surface irregularities or part position repeatability makes vacuum impractical, call the Automation experts at Cross to determine if a pneumatic gripper is right for your application.