Considering Flexible Automation? Try Our Complexity Calculator
We know many companies are considering flexible automation solutions to solve a variety of challenges such as labor shortages and safety concerns. Cobots are a type of flexible automation solution that boast easy deployability and the potential to be repositioned and repurposed within your facility. While some might believe that anyone can deploy a cobot due to its simple interface, setting up a dependable and consistently functioning cobot cell might still require the expertise of a skilled programmer.
All the clever stuff in food processing happens when the raw ingredients come together to make something yummy. But no matter how good your product is, if you can’t get it into a box and onto a store shelf, it doesn’t matter. In the past, food manufacturers relied on humans to fulfill this essential but repetitive task. With the labor shortages we now face, keeping these positions staffed is difficult, if not impossible.
Luckily, food packaging, from the production line to the box and from a box to a carton, are excellent opportunities to automate with a cobot. As the name implies, cobots are designed to collaborate with and work alongside your existing workforce. Even with mounting hardware, their footprint is compact and flexible, meaning they can be deployed on existing production lines or new ones.
But where to start? Do you buy a cobot and integrate it yourself? Do you hire an integrator? Something in between? The experts at Cross Automation built this complexity calculator to help you decide. Simply rate your application on a scale of 1 to 10 in areas like throughput, reach, payload and connectivity to discover the best path to automating your dull, dirty or dangerous tasks.
Finally, gripper technology has improved significantly in the past five years, enabling cobots to pick up things like eggs, tortillas and bread which would have been impossible previously. Vacuum technology, finger grippers and force sensors can be combined in many ways for a number of different applications.
While using a cobot to automate food packaging makes sense, it’s not necessarily easy. The robot needs to communicate with the existing machinery and, to take full advantage of its flexibility, be programmed for multiple SKUs. Engaging an experienced integrator is essential for a successful and efficient deployment.
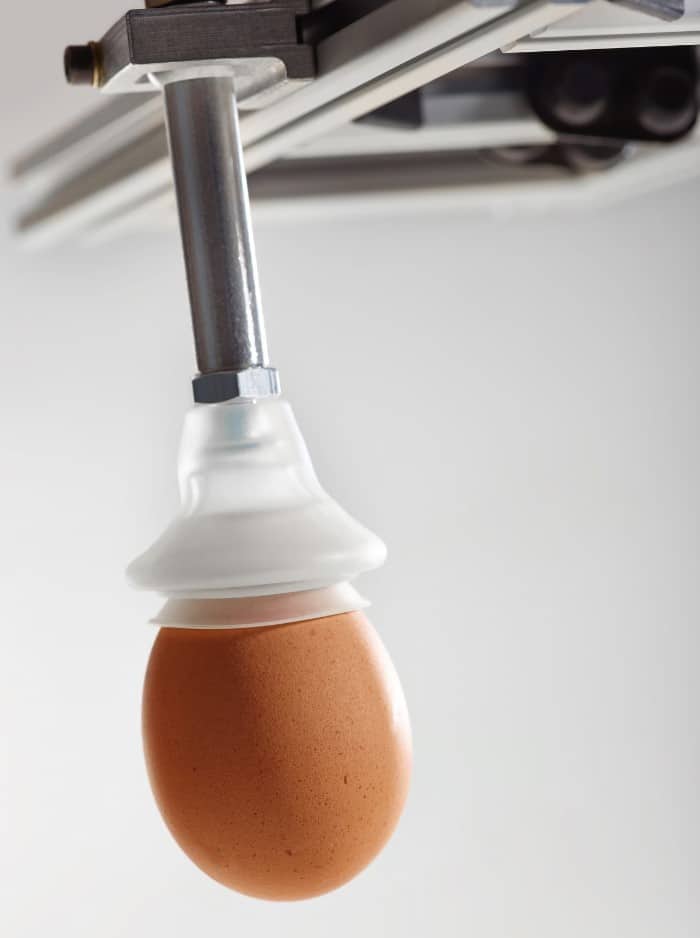
Cross Company has been working with collaborative robots since 2013. We work with several different manufacturers of robots and end-of-arm tooling which allows us to choose the right combination that is exactly suited for a particular application. We also have extensive experience in the food industry, meaning we know the sanitary, safety and economic challenges you face.
Contact Cross today to see how we can help you automate your food packaging.
Clean out your truck scale before it freezes
The kids are back to school, the days are getting shorter and the leaves are starting to change. Yep, summer is officially over and fall is well underway. Which means that it’s the perfect time to make plans for cleaning out your truck scale before winter sets in and the weather dips below freezing.
Truck scales are almost always outside and pretty much always used in bulk weighing scenarios. This means that not only can product accumulate under or around your scale, but you’re likely to get dirt and the aforementioned leaves too. If this debris freezes, it can make your truck scale completely inoperable by locking critical suspension components or joints designed to flex, impacting accuracy and functionality.
Before your first freeze, it’s very important to make sure your truck scale is clean and clear of debris. Look under your scale and clear out debris with a hose or pressure washer. Ensure that your I-beams are clear of any dirt and debris to prevent deterioration. Check the clearance between the end of your scale and the approach bulkhead to ensure that there are no trapped debris. Finally, inspect the edges of your scale deck by lifting any t-stripping and clearing away dirt and rocks that may have become trapped.
No time to do a thorough cleaning? Or don’t have the right people or ones who are willing to do it? Contact Cross Precision Measurement. We have over 80 years of experience with truck scales so you can count on us to make sure your scale is clean and weighing accurately.
What's New at Cross
New Gas Detection Partner: RKI Instruments
Cross Process Solutions is proud to announce that we have partnered with RKI Instruments to sell their fixed and portable gas detection products.
RKI is a wholly owned subsidiary of Riken Keiki, the largest gas detection and sensor manufacturer in the world. RKI offers a variety of wireless and wired fixed and portable gas detection solutions, as well as equipment for potentially explosive atmospheres and non-explosive for a variety of industries and gases.
The Cross Process Solution team is also highly experienced in all types of gas detection solutions. Get in touch today to talk about your particular application.
Did you know?
Cross creates custom software for scale indicators
In many food processing businesses, scales are critical to quality, productivity and revenue. A scale indicator is the smarts behind the scale. Indicators connect to one or multiple scales and, at their simplest, provide the operator with weight information.
However, this is just a fraction of what a scale controller can do. They can also:
- Record weight and other identifying information about a weighment locally
- Transmit that data to ERP and/or quality systems for record keeping and billing
- Control complex processes like:
- Automatically blend or batch ingredients for precise recipe formulation
- Monitor liquid or gas filling
- Precision dosing
- Truck scale unattended kiosks and much more….
In fact, the most advanced of them control multiple processes so are more properly called scale controllers. Cross has over 75 years of experience programming scale controllers to do precisely what an application calls for. From custom truck scale kiosks to multiple fiber blending lines and everything in between, our software engineers work with customers to understand their process and then program the controller to work efficiently and effectively.
Do you have an existing scale/controller combination but your process has changed so it’s no longer effective? Cross’s software engineers can work with you to update the controller’s programming to match your current process. We have experience with a wide range of brands and their programming languages. Give us a call if your scale system needs to be updated.
Cross Provides Tangible Value for You
Improve Efficiency
Sometimes the little things can make your work just a bit easier. Like the new CSR 425 retractable holder for ball valves from Cross partner M4Knick. Designed specifically to work with 1″ process connections, it allows for the easy insertion and retraction of pH sensors under process conditions.
The CSR 425 is ideal for quick-disconnect sensors. You will never have to pull the cable completely through the fitting when changing out the sensor. It also allows you to easily replace old sensor technology as well as an option for applications requiring insertion depths of up to 11.5″.
Reduce Risk
Mixing your own agricultural or cleaning chemicals from concentrates? Be sure to mix them safely and effectively by accurately measuring the ratio of chemical to water.
Oval gear chemical meters from Cross partner Flomec allow you to adjust blends to accommodate changing conditions and the amount of area to be covered while still ensuring your chemicals are strong enough to get the job done. An accurate and repeatable amount of concentrate helps reduce the possibility of over-saturation in your blend, reducing possible burn or damage. Using concentrates saves money and also takes up less space than pre-mixed chemicals.
Reduce Risk
Running forklifts or other types of equipment in your cold storage facility? Be sure to reduce the risk of hose failure by using hydraulic and industrial hose specifically developed for cold temperature applications.
A good choice is the 53DM hose from Cross partner Parker. It can operate in temperatures as low as -70° and has a matte cover for low coefficient of friction, making it ideal for over-the-sheave applications. Parflex low temperature hoses also feature a 10%-30% smaller outside diameter than rubber and are up to 70% lighter.