Grippers used in automation vary greatly in size and shape. They can be as small as a pencil eraser, or as large as a car. The largest standard grippers on the market are capable of handling several hundred pounds. But what if you need something bigger? What if you are handling 1,500 lbs? Or what if the part is 10 feet long? Luckily, there is a solution.
A gripper is essentially a self-centering clamp. It provides a means of generating clamping force while synchronizing the jaws so that they move together. The gripper must also provide a bearing system to handle the weight of the part, as well as the moments generated due to the gripping force. Most of the grippers on the market are actuated pneumatically and they use various methods to synchronize the jaws such as a wedge hook or rack-n-pinion.
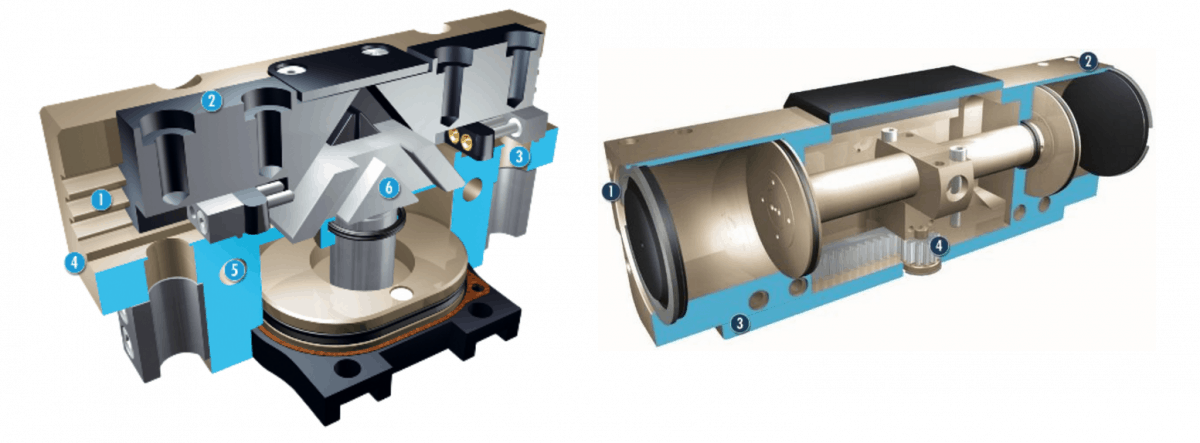
Actuating a Large Gripper
One answer to creating a really large gripper is to use a ball screw actuator. It’s easy to find an actuator with enough thrust force (large diameter screw) and enough bearing load capability (large square rail bearings), but we still need to synchronize the jaws. The answer to that is to use an opposing thread screw. This means that the first half of the screw is a right-hand thread, and the second half of the screw is a left-hand thread. When the motor turns the input shaft, the carriages will move in equal and opposite direction. Now we have the perfect recipe for a really large gripper.
The next step is to pick the right sized actuator to make the gripper. The thrust rating of the screw is directly proportional to grip force. The moment load rating of the carriages can be used to determine if the gripper is able to handle to loading caused by the weight of the part and the loading caused by the clamping force. Ultimately, big parts need a big gripper, and that is not a problem for a ball screw gripper. Below are some application examples showing fairly large ball screw gripper.
Advantages of a Screw-Driven Gripper
Video courtesy of Acieta in Council Bluffs, Iowa.
This gripper is handling wheel rims for tractors. The large wheel rim weighs 350 lbs and is about 52” in diameter. The smaller wheel rim is only 13” in diameter. This application shows the great stroke range available with these grippers, and also the great moment load capability. The gripper is powered by a servo motor that is controlled by the robot controller. It is an auxiliary axis on the controller and it can be programmed directly from the teach pendant. Having a servo run the gripper allows for position control and some force control. The jaws can be pre-positioned between moves and the force can be limited so the gripper doesn’t squeeze any more than it has to.
Another benefit of using a ball screw gripper is a high mechanical advantage for the motor. Most of these grippers are employed with 5mm lead ball screws and a 3:1 reduction in the belt and pulley drive system inside the motor wrap. That translates to a very high mechanical advantage. Just a few in-lbs of torque at the motor translates to thousands of pounds of thrust at the gripper fingers. That means you don’t need a huge motor to grip very heavy objects. The downside is that a high mechanical advantage will make jaw travel fairly slow. Most of these applications are not very high speed, so it’s an acceptable trade-off. Another nice feature of a ball screw gripper is the ability to customize the length and carriage position. If you are gripping a part that is six feet wide, then if would be nice if the carriages opened up to that six-foot mark so your finger design is simpler and they only need to protrude out straight. This is no problem with a ball screw gripper but almost impossible with any other gripper.
Looking for a gripper for heavy loads? Cross’s Automation experts can help you to select the correct option. Contact us today to discuss your particular application.