Zek Grantham | October 23rd, 2018
Not all motors are created equal. This is important to remember when picking out a motor for your hydraulic system. Each style of hydraulic motor (gear, vane, geroler, piston) has different running torque and efficiencies that must be considered. When picking out a hydraulic motor, it is a common and costly mistake to conflate the motor starting torque and its running torque.
Every motor has a maximum torque rating that is published and this is typically how most people determine if the motor will work in their application. You must know the required torque to run your system, but you cannot simply select a motor based on it’s rated maximum torque range.
Each motor should have a published torque curve like the one shown below in Figure 1 or a chart that correlates torque to flow and pressure shown in Figure 2. As you can see, the starting torque is lower than the running torque.
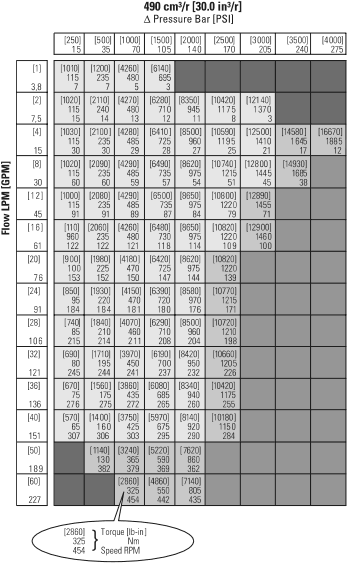
Some systems can have a motor that performs as desired in one environment, but when something as simple as the angle the system is sitting on changes, the motor can stall. This is because the amount of force acting against the motor (system requirements) alters the starting torque value. This is why you need to fully understand all the parameters of the system and how it will be operated.
A motor’s efficiency is a very important key in its starting torque. For example, while a vane motor has a very high efficiency when running at full speed, it does not have the same efficiency at lower speeds. Therefore, the starting torque is much worse than its running torque The operating speed of your system is also a very crucial factor to consider and you should understand the torque output and efficiency it will have while running. Gear, vane, and geroler motors typically have the worst starting torque due to their poor efficiencies at low speeds. A piston motor has great efficiencies in both low and high-speed applications and typically has the best starting torque.
Another key point to consider when picking out a motor for your application is how the efficiency of your motor will last over time. Each style of motor has different properties in how they function, which can be good and bad for the volumetric efficiency of that motor. For example, if you decide that a gear motor has both the right amount of starting and running torque for your system to operate, you will need to take into consideration that the efficiency of that motor is going to gradually decline over the course of its life.
The way gear motors function requires the gear teeth to engage one another which inevitably causes wear on the gears. This wear results in a higher internal leakage, meaning it is less efficient and the amount of available starting and running torque decreases. So even though your motor runs your system to the desired results when it is first put into the field, it may not run the system a year later due to this loss in efficiency.
On the other hand, a vane motor keeps its efficiency throughout its life, up until catastrophic failure occurs. This is because of the way the vane motor functions, with each vane extending out of its sleeve during rotation, the design compensates for wear. Each vane in the motor can wear down over time but still keep its efficiency because the vanes will continue to extend out further as they wear down, decreasing the risk of leakage.
But with high efficiencies comes added cost. This is why understanding your applications torque requirements, both starting and running torques is key to picking out the ideal motor for the application that is both cost-effective and able to run the system.