Metrology Glossary: Checkweigher
What Is A Checkweigher?
A checkweigher functions as an automated or manual device used for gauging the weight of packaged goods, verifying their conformity with predetermined weight parameters. Primarily used in fast-paced production environments where manual weighing proves impractical and time-consuming, this equipment plays an important role. Its core purpose lies in the detection of products that fall below or exceed the specified weight thresholds. This capability significantly contributes to upholding the overall quality and consistency of products, consequently safeguarding consumer satisfaction.
What Are Checkweighers Used For?
Quality Assurance:
- Compliance Verification: Checkweighers ensure compliance with weight standards, preventing underfilling and overfilling to avoid customer dissatisfaction and regulatory issues.
- Waste Reduction: By identifying underfilled and overfilled products, checkweighers minimize product giveaway and waste, leading to cost savings for manufacturers.
- Consistency: Consistent product weight builds trust, enhancing brand reputation and reliability.
Inventory Control:
- Accurate Tracking: Checkweighers provide precise data on product weight and quantity, crucial for efficient inventory management.
- Process Optimization: Recognizing product weight trends, checkweighers optimize production and packaging, improving efficiency and reducing costs.
- Cost Reduction: Accurate weight data prevents overfilling, saving on packaging and shipping costs, while identifying underfilled products avoids complaints and recalls.
Food Safety:
- Contaminant Detection: Some checkweighers include detectors, ensuring the removal of contaminated items for food safety.
- Regulatory Compliance: Checkweighers play a vital role in meeting food safety regulations by ensuring accurate product weighing.
Production Efficiency:
- Increased Throughput: Operating at high speeds, checkweighers increase production speed and throughput, resulting in cost savings and increased profitability.
- Reduced Downtime: Automated checkweighers eliminate manual weighing, reducing downtime and labor costs.
- Enhanced Efficiency: Streamlining the packaging process and minimizing errors, checkweighers contribute to overall production efficiency.
Data Analysis:
- Trend Identification: Checkweighers collect data on product weight, aiding in the identification of trends and patterns in the production process.
- Process Improvement: Analyzing weight data helps address issues affecting product quality, improving overall process control.
- Informed Decision-Making: Utilizing weight data for decisions enhances efficiency, reduces costs, and ensures product quality through a data-driven approach.
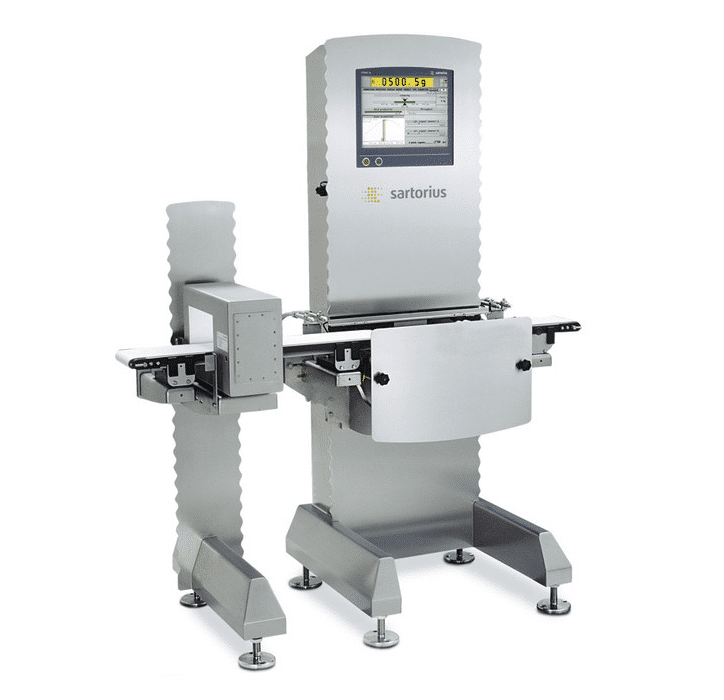
Related Terms
Average piece weight (APW) indicates the mean of the weight carried by each individual item within a specified set of items....
A weighing scale, also known as a mass scale, weight scale, mass balance, or weight balance, is a crucial device used for the precise determination of an object's weight or...
A bench scale is a weighing device commonly used within laboratory or industrial environments. Typically designed as a compact unit for placement on a table, it incorporates a platform or...